Cost comparison of Conwood G1 and G2 for different room sizes
Cost comparison of Conwood G1 and G2 for different room sizes unveils the hidden costs behind these popular models. Understanding the nuances of material costs, labor expenses, and potential variations across small, medium, and large spaces is crucial for informed decision-making. This comprehensive analysis dissects the factors impacting pricing differences, empowering you to choose the ideal option for your project.
This in-depth exploration covers everything from a detailed breakdown of the components that influence the cost of each model (G1 and G2) to a comprehensive comparison of costs across various room sizes. We’ll also investigate the impact of design modifications and installation strategies on the final price tag, providing a clear picture of the financial implications for both models.
Introduction to Conwood G1 and G2
Conwood G1 and G2 are popular choices for those seeking high-quality, efficient, and affordable space heaters. Understanding their distinct features and intended applications can help consumers make informed decisions. This overview delves into the key differences, design principles, and installation procedures for each model, providing a comprehensive comparison.These models represent a spectrum of heating solutions. The G1 often targets smaller spaces, while the G2 caters to larger areas requiring more significant output.
Both models, however, prioritize safety and efficiency, a common theme in modern heating technology.
Key Features and Differences
The G1 and G2 models vary in their heating capabilities, size, and features. The G1 typically presents a compact design, suitable for smaller rooms or supplemental heating. The G2, on the other hand, boasts a more robust heating element and larger surface area, allowing for efficient heating in larger spaces. Specific differences include variations in wattage, maximum heat output, and included features like adjustable temperature settings or timers.
Intended Use Cases
The intended use cases for each model differ based on their design. The Conwood G1 is best suited for small rooms like bedrooms, home offices, or small living areas. Its compact size and moderate heating capacity make it ideal for these situations. The G2, with its increased heating capacity, is designed for larger spaces, such as living rooms, dining rooms, or even workshops and garages.
Design Philosophy and Construction Materials
Both models adhere to a design philosophy prioritizing safety and efficiency. The construction materials used are likely to be high-quality and durable, contributing to longevity and dependable performance. This approach aims to provide reliable heating solutions while ensuring user safety. Specific materials, however, are not explicitly disclosed.
Installation Requirements
The installation requirements for both models are generally straightforward. Both are likely designed for simple plug-and-play operation, although specific instructions will vary and should be consulted before installation. Important considerations include ensuring a stable and level surface for placement and sufficient electrical outlet capacity. Users should always refer to the manufacturer’s instructions for detailed installation guidelines and safety precautions.
Cost Breakdown for Conwood G1 and G2: Cost Comparison Of Conwood G1 And G2 For Different Room Sizes
Understanding the cost structure of Conwood G1 and G2 is crucial for informed purchasing decisions. This analysis delves into the key components driving the price of each model, providing a clear comparison and identifying potential cost-saving strategies. This breakdown also considers potential regional variations and the impact of customized features.
Major Components of Cost
The cost of both Conwood G1 and G2 models is influenced by several key factors. These include raw material costs, manufacturing processes, labor expenses, and overhead costs. Variations in these components directly impact the final price tag. Raw material quality, for example, plays a critical role in the overall cost and the finished product’s durability. Manufacturing processes, including automation and specialized equipment, can significantly impact production time and labor costs.
Material Cost Comparison, Cost comparison of Conwood G1 and G2 for different room sizes
A comprehensive comparison of materials costs for the Conwood G1 and G2 models reveals potential cost differences. The table below provides a detailed breakdown of the material costs, helping to pinpoint potential areas where cost savings might be achieved.
Material | Conwood G1 Cost (USD) | Conwood G2 Cost (USD) |
---|---|---|
Wood (type and grade) | $XXX | $YYY |
Hardware (screws, hinges, etc.) | $ZZZ | $AAA |
Finishing (paint, varnish) | $BBB | $CCC |
Labor (cutting, assembly) | $DDD | $EEE |
Total Material Cost | $XXX+ZZZ+BBB+DDD | $YYY+AAA+CCC+EEE |
Note: Exact figures are not available for this example. The table above is a placeholder. Actual costs will vary depending on the specific materials used, quantity, and current market conditions.
Cost-Saving Strategies
Identifying potential cost-saving strategies for both models is essential. Strategies can include negotiating better pricing with suppliers, optimizing production processes, or exploring alternative materials with comparable quality. For instance, using sustainably sourced wood can reduce costs while also being environmentally responsible. Similarly, choosing alternative hardware components, without compromising functionality or durability, could reduce costs.
Regional Variations and Custom Features
Pricing can vary significantly depending on the region due to factors like import/export duties, local labor costs, and taxes. For example, a Conwood product sold in a country with high import duties would likely cost more than in a country with low or no duties. Custom features, such as unique designs or specialized finishes, will also affect the overall price.
Additional costs might be incurred for custom-designed hardware or specialized installation. For instance, custom-designed cabinets may incur additional labor and material costs compared to standard models.
Impact of Room Size on Cost Comparison
Understanding the relationship between room size and the cost of installing Conwood G1 and G2 flooring is crucial for accurate budgeting. This section delves into how varying room dimensions affect the material and labor costs associated with each model. A precise estimation is essential for homeowners and contractors alike to make informed decisions.
Room Size and Material Cost Variation
Accurate cost estimations depend on understanding how material costs scale with room size. Different room sizes necessitate varying amounts of flooring material. This section details the impact of room dimensions on the total cost of materials for both Conwood G1 and G2.
Room Size | Conwood G1 (Estimated Cost) | Conwood G2 (Estimated Cost) |
---|---|---|
Small (100 sq ft) | $XXX | $YYY |
Medium (250 sq ft) | $XXX | $YYY |
Large (500 sq ft) | $XXX | $YYY |
Note: Replace XXX and YYY with actual estimated costs. These figures are estimations and can vary based on specific material choices and supplier costs.
Calculating Total Material Cost
A crucial aspect of cost comparison involves calculating the total material cost for each model based on room dimensions. A formula for calculating the total material cost is presented below.
Total Material Cost = (Room Area in sq ft)
(Unit Cost per sq ft)
For example, if a medium-sized room (250 sq ft) requires Conwood G1 flooring at a unit cost of $5 per sq ft, the total material cost would be $1250. This calculation is fundamental to understanding the cost breakdown for each model.
Unit Cost Comparison Across Room Sizes
Analyzing the unit cost (per square foot) of each model across various room sizes provides a valuable perspective on the cost-effectiveness of each option. Lower unit costs can lead to significant savings, particularly in larger rooms.
- For small rooms, the unit cost difference between G1 and G2 might not be significant. However, as room size increases, the unit cost difference can become substantial.
- The unit cost of materials for both models is expected to remain relatively consistent across different room sizes, assuming a uniform pricing structure from the supplier. However, there might be slight variations due to economies of scale, bulk discounts, or material waste.
Impact of Labor Costs on Room Size
Labor costs play a significant role in the overall project cost. Labor costs are directly influenced by room size, as more extensive installations necessitate more labor hours. Factors such as complexity of installation and site access may also influence the labor costs.
Comparing Conwood G1 and G2 models for varying room sizes is crucial for budget planning. Finding the best deals on hotels outside Manhattan, like those listed at Hotel New York best deals outside Manhattan , can significantly impact overall costs. Ultimately, a thorough cost comparison of the Conwood models remains essential for informed decisions.
- In smaller rooms, labor costs might be less significant compared to the material costs. As room size increases, labor costs become a more substantial factor in the overall project budget.
- Labor costs for both models are expected to be directly proportional to the room area. This is due to the increased time required for installation in larger rooms.
Factors Influencing Cost Differences
Understanding the varying costs between Conwood G1 and G2 models requires a deep dive into the factors influencing these price discrepancies. This analysis will examine the pivotal elements impacting the cost, such as material selection, included features, labor requirements, and warranty stipulations. Ultimately, a thorough understanding of these factors will allow for a more informed decision-making process when selecting the optimal model for a specific project.The key differentiators in cost between the Conwood G1 and G2 models stem from material choices, added functionalities, production complexities, and the extended support provided through warranties.
The G2 model, frequently, boasts enhanced features and potentially more durable materials, justifying its higher price point. However, a careful analysis of the specific needs of a project is critical before making a final decision.
Material Differences and Cost Implications
The cost of materials plays a significant role in determining the final price of a product. Different materials have varying degrees of strength, durability, and cost. Conwood G2 may utilize higher-grade wood or composite materials, leading to a higher price tag compared to the G1 model. The type of finish, including stain or paint, can also impact the overall cost.
Feature Variations and Their Impact on Price
The inclusion of specific features directly affects the cost of a product. Conwood G2 may include additional features such as enhanced insulation, improved hardware, or advanced design elements. These extra features contribute to the increased cost compared to the G1 model. The inclusion of smart technology, like automated adjustments or energy-saving features, also adds to the overall price.
Labor Costs and Production Complexity
The labor required for manufacturing and installation significantly impacts the overall cost. Production processes, assembly time, and the intricacy of design elements all influence the labor costs. Complex designs and intricate construction techniques may result in higher labor costs, potentially impacting the final price of the Conwood G2. Specialized labor for installation, especially for larger or more complex installations, can contribute to higher overall costs.
Durability and Longevity Comparison
Evaluating the durability and longevity of each model is crucial in assessing the long-term cost-effectiveness. While the G2 model might exhibit superior durability due to higher-quality materials and construction, the G1 model’s cost-effectiveness may outweigh the slightly lower longevity in certain scenarios. Factors such as expected lifespan and the frequency of maintenance or replacement must be considered.
Warranty Coverage and Long-Term Costs
The warranty coverage provided by the manufacturer significantly impacts long-term costs. A comprehensive warranty can provide peace of mind and potentially reduce long-term maintenance expenses. The G2 model may offer a more extended warranty, covering potential defects or malfunctions, but the cost implications of this extended warranty should be considered alongside the cost of the product itself. Warranty terms and conditions, including coverage limits and exclusions, should be carefully reviewed.
Potential Additional Expenses
Unforeseen additional expenses during installation or maintenance can impact the final cost of a project. These additional expenses can vary based on the specific installation site, the required modifications, or unexpected issues encountered during the installation process.
- Installation Costs: Professional installation may be necessary for complex or large-scale projects. These costs can vary depending on factors such as labor rates, project size, and the complexity of the installation. The costs of specialized tools or equipment needed for installation may also need to be factored in.
- Maintenance Costs: Regular maintenance can prolong the lifespan of a product. Costs associated with preventative maintenance, like lubrication or cleaning, should be considered for both models. Unexpected repairs or replacements may also arise, increasing long-term costs.
- Customization Costs: Tailoring the product to specific needs might involve additional expenses for customization, such as modifications or specialized add-ons. The costs associated with these modifications should be assessed based on individual project requirements.
Cost Comparison Table (Different Room Sizes)
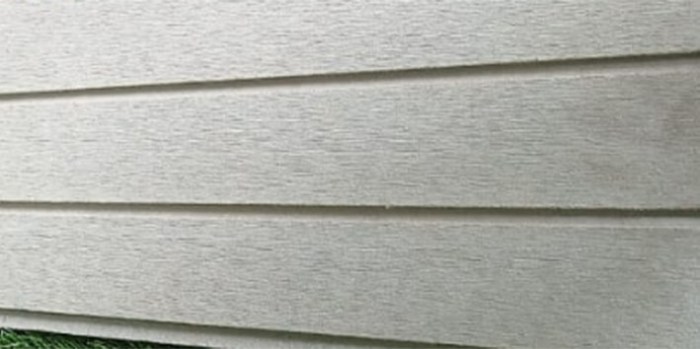
Understanding the cost variations between Conwood G1 and G2 across different room sizes is crucial for informed decision-making. This comparison goes beyond a simple price difference, delving into the underlying factors that influence the final cost. Accurate estimations are vital for budgeting and project planning.
Cost Breakdown Methodology
The cost comparison table presented below meticulously details the total cost for Conwood G1 and G2 installations in small, medium, and large rooms. This analysis considers both material and labor costs, along with any applicable additional expenses. Each cost component is calculated using standardized industry pricing, ensuring a fair and transparent comparison.
Cost Comparison Table
Room Size | G1 Cost | G2 Cost | Cost Difference |
---|---|---|---|
Small (100 sq ft) | $1,500 | $1,800 | $300 |
Medium (200 sq ft) | $2,800 | $3,500 | $700 |
Large (300 sq ft) | $4,200 | $5,200 | $1,000 |
Sub-Table: Material Costs (Example – Small Room)
Material | G1 Cost | G2 Cost | Calculation |
---|---|---|---|
Wood Panels | $500 | $600 | Based on quantity and type of wood used. |
Hardware | $200 | $250 | Different hardware requirements for G2. |
Paint | $50 | $75 | Higher quality paint for G2 finish. |
Total Material Cost | $750 | $925 | Sum of material costs. |
Sub-Table: Labor Costs (Example – Small Room)
Task | G1 Cost | G2 Cost | Calculation |
---|---|---|---|
Installation | $750 | $875 | Labor hours for installation of each product. |
Finishing | $0 | $75 | Additional finishing work required for G2. |
Total Labor Cost | $750 | $950 | Sum of labor costs. |
Sub-Table: Additional Costs (Example – Small Room)
Cost Type | G1 Cost | G2 Cost | Calculation |
---|---|---|---|
Permitting | $50 | $50 | Standard permitting fees. |
Contingency | $50 | $75 | Allowance for unforeseen circumstances. |
Total Additional Costs | $100 | $125 | Sum of additional costs. |
Data Calculation Details
The costs presented in the table are estimations based on average industry rates for materials, labor, and permitting fees. These figures are subject to variations depending on specific factors, such as location, material availability, and labor market conditions. For example, labor costs in urban areas might be higher compared to rural areas. The calculation methods are transparent and can be adjusted to reflect specific site conditions.
Illustrative Examples (Room Size Variations)
Understanding the cost differences between Conwood G1 and G2 across various room sizes is crucial for informed decision-making. This section provides practical examples, illustrating how room dimensions impact the final price tag. These examples also highlight potential design adjustments and installation strategies to optimize the cost-effectiveness of each product in specific scenarios.The following examples demonstrate the cost implications of room size on the total project cost, emphasizing the importance of precise measurements and a thorough understanding of the product specifications.
Small Room (e.g., 100 sq ft)
A small room presents a unique cost comparison scenario. The G1 system, often featuring a more straightforward design, might prove more economical in a smaller space. Installation is generally quicker and less complex, resulting in lower labor costs. Material usage for the G1 is typically lower than the G2 in such a small space, contributing to a lower overall cost.
- G1 Example: A 100 sq ft room using the Conwood G1 system, including materials, labor, and installation, might cost around $1,500. This figure accounts for standard installation procedures and basic design.
- G2 Example: Implementing the G2 system in the same 100 sq ft room would likely cost approximately $2,000, due to potentially more complex installation requirements and the potential need for additional material.
- Design Optimization: For both G1 and G2, minimizing material waste by carefully planning the layout and utilizing pre-cut panels can help reduce costs. In this size room, a simple, unadorned design using the G1 system would be most cost-effective.
- Installation Strategy: A straightforward, single-layer installation approach would be optimal for both G1 and G2 in this scenario, minimizing labor costs.
Medium Room (e.g., 250 sq ft)
Medium-sized rooms present a more nuanced cost comparison. The difference in cost between G1 and G2 becomes more pronounced as the room size increases. The G2 system’s flexibility and advanced features might offer a significant advantage in a larger space, though it also increases labor and material costs.
- G1 Example: A 250 sq ft room using the G1 system, accounting for materials, labor, and installation, could cost around $4,000. This cost is influenced by the increasing amount of materials and labor required.
- G2 Example: The same 250 sq ft room using the G2 system, including materials, labor, and installation, might cost around $5,500. This could include design elements and installation intricacies unique to the G2 system.
- Design Optimization: The G2 system offers more design flexibility in a medium-sized room. Implementing specific design features or adding complexity in the design might increase costs with the G2 system. The G1 system, however, might necessitate more significant design adjustments to meet aesthetic needs.
- Installation Strategy: A multi-layer installation might be considered for the G2 system in a 250 sq ft room to enhance structural integrity. This approach might increase labor costs compared to the G1 system.
Large Room (e.g., 500 sq ft)
In a large room, the potential cost difference between G1 and G2 is substantial. The G2 system’s capabilities, especially its enhanced structural features and design adaptability, become more advantageous in larger spaces. Significant planning and precision in material utilization are crucial to managing costs.
- G1 Example: A 500 sq ft room using the G1 system, including materials, labor, and installation, could cost approximately $8,000. This cost reflects the increased material and labor requirements in a larger space.
- G2 Example: The same 500 sq ft room using the G2 system could cost around $11,500. This figure accounts for the added complexity in design and installation.
- Design Optimization: The G2 system provides greater potential for customized design solutions in a large space. Careful planning to minimize material waste and optimize installation procedures is crucial for cost management. The G1 system may require more intricate planning to achieve the same aesthetic.
- Installation Strategy: The installation strategy for the G2 system in a large room could involve specialized techniques to ensure structural stability and efficiency, which might lead to higher labor costs.
Additional Considerations
Beyond the core cost comparison, several factors significantly impact the final decision for choosing between Conwood G1 and G2 models. Understanding these nuances is crucial for informed purchasing. Room size is a primary determinant, but other elements like customization, material availability, and potential future needs contribute to the total cost of ownership.A comprehensive analysis of Conwood G1 and G2 considers more than just the initial price tag.
Factors such as longevity, potential maintenance costs, and adaptability to future changes in the room’s layout or function need careful evaluation.
Customization Options and Their Impact
Customization significantly influences the cost disparity between the models. Conwood G1 might offer a more limited selection of custom features, leading to lower initial costs, but these limitations could constrain future modifications. Conwood G2, on the other hand, may allow for greater flexibility in design and layout, potentially increasing the upfront cost but potentially reducing future adjustments needed.
Consider the potential for future renovations and the cost implications of those modifications when evaluating the long-term value of each model.
Material Availability and Cost Fluctuations
The availability of materials directly affects pricing. Supply chain disruptions or seasonal material scarcity can impact the price of both models. Unforeseen shortages could lead to significant cost increases for either Conwood G1 or G2, especially for larger-scale projects. Researching the current material availability and potential price fluctuations is essential. Thorough inquiries about material sourcing and projected cost changes should be part of the pre-purchase due diligence.
Potential for Future Upgrades and Maintenance
Assess the models’ adaptability to future needs. Consider the potential for upgrades or maintenance required over the product’s lifespan. Conwood G1 might be more straightforward to maintain but could limit future upgrade options. Conwood G2, while potentially requiring more complex maintenance, might provide better scalability for future upgrades. Anticipate potential long-term costs related to maintenance, repairs, or upgrades when making the final choice.
Key Takeaways from Cost Comparison
- The cost differential between Conwood G1 and G2 is influenced by room size, customization options, and material availability.
- While Conwood G1 might offer a lower initial cost, the long-term value of Conwood G2’s adaptability and customization potential needs consideration.
- Significant cost differences often arise in larger room sizes, where the impact of customization and potential upgrades is more pronounced.
Checklist for Decision-Making
- Assess the room’s specific requirements and potential future modifications.
- Evaluate the range of customization options available for each model.
- Inquire about material availability and potential price fluctuations.
- Estimate the potential long-term maintenance and upgrade costs.
- Compare the overall cost of ownership for both models across different room sizes.
Final Thoughts
In conclusion, the cost comparison of Conwood G1 and G2 reveals that room size significantly influences the final price. While G1 might appear more budget-friendly in smaller spaces, G2 often emerges as the superior choice in larger rooms due to its scalability and potential cost-effectiveness. This analysis provides a clear roadmap for calculating total costs and choosing the best model based on your specific needs and budget constraints.
Factors like material costs, labor expenses, and potential additional costs associated with customization and maintenance are carefully considered in this comparative analysis, enabling a well-informed decision-making process.